4.8 Quality management
Quality can be seen from a number of different perspectives. In terms of marketing, if there is a customer perception of quality there will be increased sales, brand loyalty and the opportunity to charge prices above those of competitors. For a consumer, it can mean that the product provided by a business:
- is reliable and durable
- is free from any defects and safe to use
- provides value for money
- does everything that the advertising claims.
For a customer-focused business, quality also means that each and every good made or provided by the business is consistent in its quality. For service-based businesses quality can be measured in terms of satisfaction with customer service.
Quality management, therefore, involves all activities to ensure that the outputs of the business are consistent, durable and reliable and meet the quality standards stated in the operations plan. In order to remain competitive in today’s business environment, a business will aim to produce a quality product or service that provides value for money.
To achieve a competitive advantage over other businesses in the same market, a business may choose as its performance objective to have products of a superior quality. If it cannot achieve superior quality, a business will strive for a certain standard of quality, because inconsistent and poor quality will be an operations cost. Customer returns, poor sales, product recalls and repairs will be significant expenses that will also damage the value of the business.
There are other external influences on quality. The government tries to ensure the quality of all goods through laws that protect consumers from unscrupulous business practices and also protect businesses from one another.
In Australia, products must be fit for the purpose for which they were intended. This means that the product must be able to do what the business claims it can do, and do it safely. This legislation includes the Competition and Consumer Act 2010 (Cth) and the Fair Trading Act 1987 (NSW). The government also requires certain businesses that provide services (such as nursing homes and builders) to be licensed or certified.
Business Bite
In 2018, new Country of Origin Labelling (CoOL) requirements for food came into force under the Competition and Consumer Amendment (Country of Origin) Act 2017. The new law requires all packaged food sold in Australia to have a label that states how much is Australian grown, produced or made. The country of origin of any imported foods must be clearly and accurately stated on the label. Misleading consumers by word or image about the origin of the food is illegal. Businesses need to ensure that their labels comply with the Act and since 1 July 2018 have been required to display the new labels.
Licence renewal will require inspections and compliance checks to be completed in order to ensure that certain standards of facilities and care are being maintained.
There are a number of strategies that businesses can use in order to achieve improved quality in both manufacturing goods and the provision of services. The three main approaches to quality management are quality control, quality assurance and quality improvement.
Quality control
It is generally agreed that good management anticipates and prevents problems before they occur. Quality will be the responsibility of a specialist quality inspector. For a business that discovers too late that it has been selling poor-quality or defective goods, the consequence will be lost customers, damaged goodwill and expensive warranty costs. A complete recall of products may be necessary and required by the government.
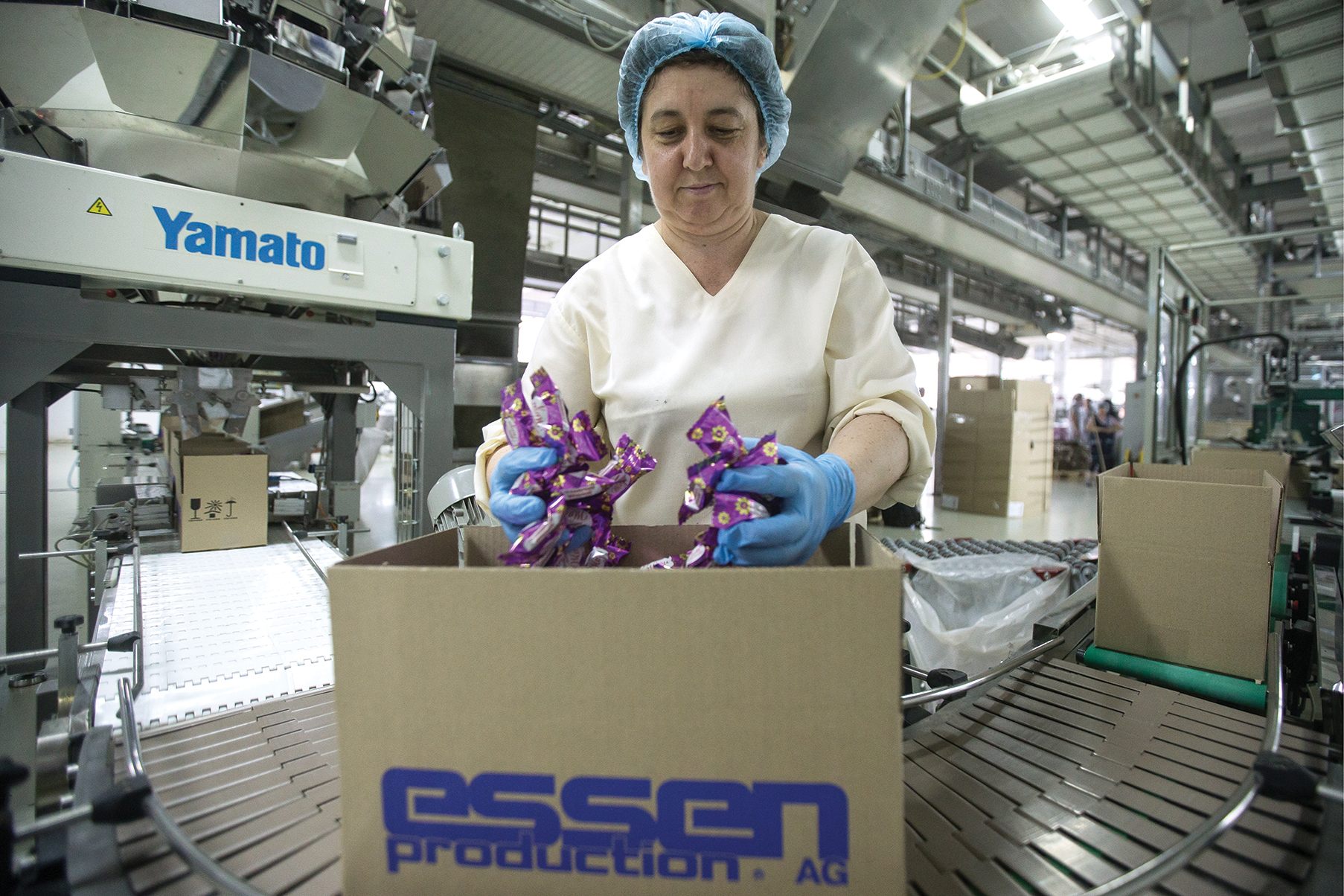
Quality control involves checking transformed and transforming resources in all stages of the production process. These controls can take place at three different stages: feed-forward, concurrent and feedback controls.
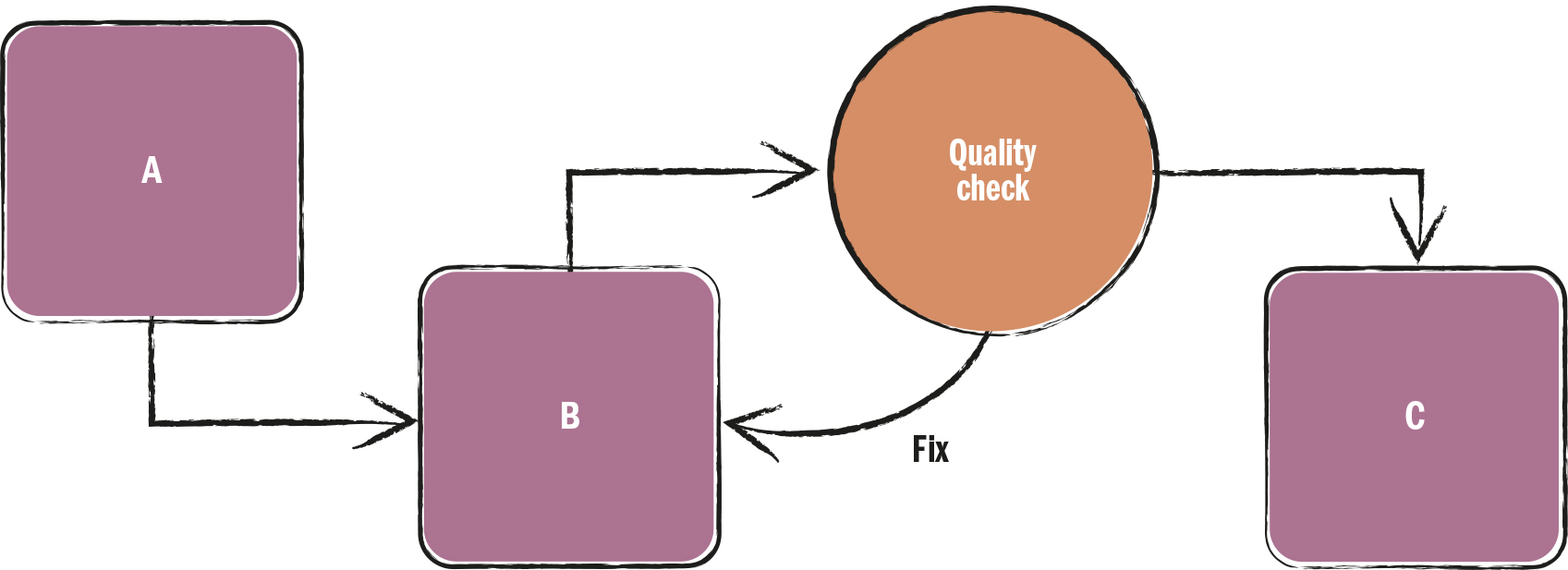
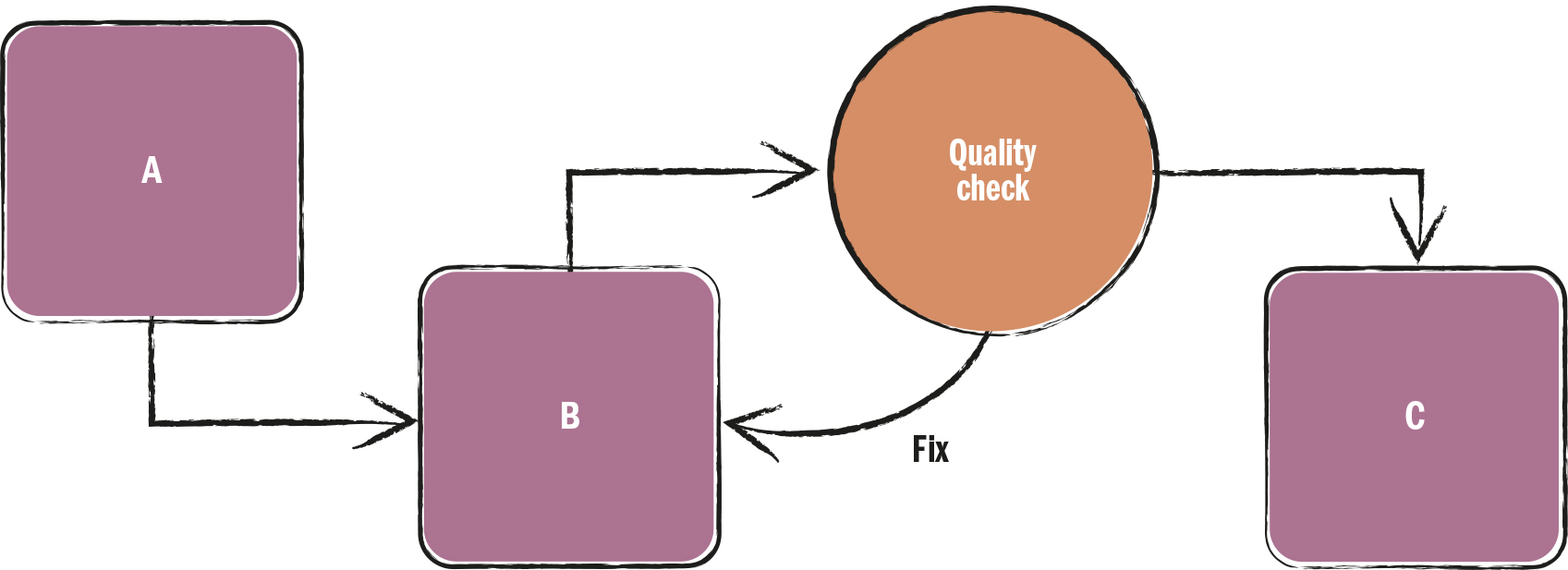
Feed-forward controls involve the use of careful planning before production begins, in order to prevent a problem occurring. Proactive management will anticipate a problem before it arises and amend the situation so that the problem does not occur. An example of a feed-forward control is a fast-food restaurant checking the size of hamburger buns on arrival from the bakery before they go to the production line. Concurrent controls are used during work in progress; that is, during the manufacturing process. This could include a soft drink manufacturer using laser beam technology to determine whether soft drink cans have been filled to the correct level. Feedback controls involve checking the final product – after production or delivery of the service is complete. In some cases, customer surveys are included with the product to try to gauge the degree of customer satisfaction with the product.
Large motor mechanic businesses often send out a letter to the client a few days after the client’s car has been serviced to thank the client and to gauge customer satisfaction with the service. In each case of quality control there is heavy reliance on the employees to complete jobs properly.
With the use of batch numbers and codes on products, firms can check where problems exist, determine the production time period involved and identify where improvements need to be made. The problem may arise at the retail end of the distribution chain; for example, inadequate refrigeration in a supermarket may result in food poisoning.
Control involves setting up procedures for evaluation and establishing standards for performance measurement. One of the main reasons for planning an activity is to achieve a particular objective or goal. Once the plan has been put into action, the whole procedure needs to be controlled and monitored. The actual performance of machinery and staff should be measured and compared with what was originally planned. A measure or standard is identified so that results can be compared. A firm may compare its performance to that of other businesses in the same industry by using the industry average as a benchmark. This provides a guide to the business’s progress. The business will then make necessary corrections or adjustments to its processes in order to achieve the desired results.
Effective benchmarking requires a business to:
- identify where quality problems are occurring
- research leading businesses in the industry
- determine the industry standard for quality
- implement changes to achieve the industry benchmark.
Businesses will try to establish why the variations have occurred and will look at both the internal and external influences. Many professional occupation associations have established standards as a control mechanism for the services they provide. These standards are often referred to as codes of practice. They set out the minimum level of service that registered members of a profession are expected to provide. These standards go beyond the rules set by the relevant legislation. Codes of practice have been set up by various professional groups in Australia, including the Institute of Chartered Accountants, the Law Society and the New South Wales Board of the Medical Board of Australia.
Business Bite
It seems that most car companies have had to contact customers to repair vehicle problems, sometimes proactively and at other times because they are required to do so by government. Brake issues, fuel leaks and sudden power loss can cause death and injury. Toyota, Audi and BMW have all voluntarily recalled vehicles in recent years for these reasons.
The second-largest automotive quality scandal had its origins in 2015 when the United States Environmental Protection Authority discovered VW diesel engines had been programmed to ‘cheat’ their emissions test. This misled customers about engine performance. An estimated 11 million cars produced by VW were affected. As a consequence, the VW Group CEO resigned and the company spent over US$7.3 billion to correct the issue.
The Takata airbag scandal quickly followed, causing the world’s biggest car recall. As of 2018, Takata airbags have been responsible for more than 230 injuries and at least 23 deaths worldwide. Four million vehicles in Australia were affected, and there was one fatality, in 2017. The government ordered a critical recall of vehicles fitted with Alpha airbags (a subset of Takata airbags). Owners of such vehicles were sent a letter strongly recommending that they stop driving their vehicles immediately and arrange for the airbag inflators to be replaced, due to the significant risk of injury or death. The website ismyairbagsafe.com.au was created so owners could check their car. As well, a prominent advertising campaign, ‘Faulty airbags? Don’t die wondering’, was used to warn customers about the danger.
Ethical spotlight 4.1
Some businesses may ignore potential problems with their products. Their research may have told them that the cost of the recall may be a lot more than the cost of legal action. Do businesses have an ethical responsibility to recall their products if they only think there may be a problem and no actual fault has been reported?
Activity 4.4 Discussion
- Describe an appropriate strategy that could have been used to prevent a quality issue.
- Explain why a firm would recall its product.
- Evaluate what advantages and disadvantages a recall could present for the firm.
Quality assurance
While quality control involves measuring quality and taking corrective action, quality assurance is much more proactive; that is, it aims to prevent quality problems before they occur. Quality assurance involves establishing and using a set of procedures and processes that will prevent product defects or errors in delivering services from occurring. Quality is ‘assured’, or guaranteed, because the whole business is focused on ensuring quality. There is more emphasis on the contribution to quality from the whole operations system and the entire business. Employee involvement through quality circles and work teams has been an effective strategy to identify and discuss quality issues, prevent development of defects and solutions to quality issues.
Quality can be guaranteed by achieving certificates for meeting quality standards from Standards Australia and AS/NZS for Australian and New Zealand Standards, and ISO (International Organization for Standardization) certification for meeting international standards. Examples of these certificates are:
- AS/NZS ISO 9001 or 9002 and 9003 – the business has satisfied these requirements and is recognised as a ‘Quality Endorsed Company’
- 9001 – indicates that the business has quality assurance in product design, development, manufacture, installation and servicing
- 9002 – indicates quality assurance in manufacturing
- 9003 – covers service-based industries.
Possession of a ‘Quality Endorsed Company’ certificate provides assurance that a quality management system is used in operations. The other advantage of obtaining a quality assurance certificate is that many businesses and government organisations will prefer to deal with businesses with proven quality systems.
Source 4.25a What ISO standards do for you (02:05)
Extra activity Comprehension and research
Answer the following questions about Source 4.25a.
- Recall how many standards ISO has.
- Recall how long ISO has been in operation.
- Use the internet to look up three of the ISO standards shown in the video. For each standard, outline:
- what the standard covers
- when it was published
- its current status
- the name of the technical committee that deals with it.
Quality improvement
The total quality management (TQM) approach to quality relies on continuous improvement in all functional areas, not just operations. It is often referred to as kaizen and is widely used in Japanese industry. Rather than correcting mistakes, controls are put in place to ensure poor-quality goods never reach the consumer. The greatest success would come from getting the process right the first time; that is, zero defects as a performance objective.
The concept of quality circles is relevant to TQM. Quality circles are regular meetings of a group of employees from different sections of the business to discuss issues arising in the workplace, even if there are no current quality issues. For example, a meeting of all staff can be called each morning to review the key performance indicators (KPIs) of the previous day’s operations. Employees are encouraged to discuss quality issues and offer suggestions. There is a focus on continuous small improvements in products and processes. It is a much more effective strategy than waiting for major improvements from technological breakthroughs. The group tries to clearly identify any problem areas and come up with possible solutions to those problems. The team leader presents its results to management for consideration, who then make the final decision about the actions to take. TQM necessitates careful review of the actions of competitors and possible innovative measures to be taken in relation to all aspects of the business.
Through benchmarking, many businesses are able to compare themselves with the rest of their industry. This allows a firm to identify critical processes that may need improvement. The firm will then study the best operational processes used by its competitors in order to select ways that the firm can improve its own methods. Through world’s best practice the firm can compare its productivity or performance with the highest standards achieved by businesses worldwide and select businesses to use as models.
Improvements in quality can be measured using KPIs. These will vary from industry to industry and are often based on industry benchmarks of what is commonly accepted in Australia (or internationally) as the standard a business should aim for. A business may even compare itself to its largest competitor. Examples of KPIs include:
- number of defects per 100 units manufactured
- number of warranty claims made by customers
- percentage of repeat customers
- number of accidents and operational incidents
- repair costs
- number of working hours lost due to breakdowns or interruptions to operations
- amount of positive customer feedback from surveys.
With improved quality a business will experience reduced operations costs, higher sales and repeat customers and hence more profit. However, it can be very costly to ensure quality; staff may need retraining and it can take considerable time and effort to change the corporate culture to being quality focused.
Quality control | Quality assurance |
---|---|
Usually at the end of operations, one person reviews the products made and checks for mistakes. Checks during the operations process may also be done. | Systems, procedures and policies are in place to prevent quality problems. No one individual is responsible for quality; everyone has a contributing role, no matter how small. |
A certain percentage of defects is allowed and set as a standard. | Quality is assured as all products are expected to pass inspection; zero defects. |
Assembly lines flow continuously unless repairs are required. | Production process can be interrupted to improve systems. |
Quality management stops once the product leaves the business. | Quality is provided through after-sales service. |
Employees are not included in quality improvement decision-making. | Employees are included in decision-making through quality circles, consultation and two-way communication. |